Industrial robot palletising is an automated system used in manufacturing and logistics to efficiently arrange products onto pallets for storage or shipping. In this process, products are fed into a designated area, known as the palletising cell, where an industrial robot equipped with specialized grippers or end of arm tooling carefully stacks them onto a pallet following a predetermined pattern.
These systems offer significant advantages over manual palletising, including increased speed, precision, and safety. Industrial robot palletising can handle heavy loads and operate consistently without breaks or fatigue. Additionally, they can adapt to various product sizes and shapes, making them highly versatile for different industries.
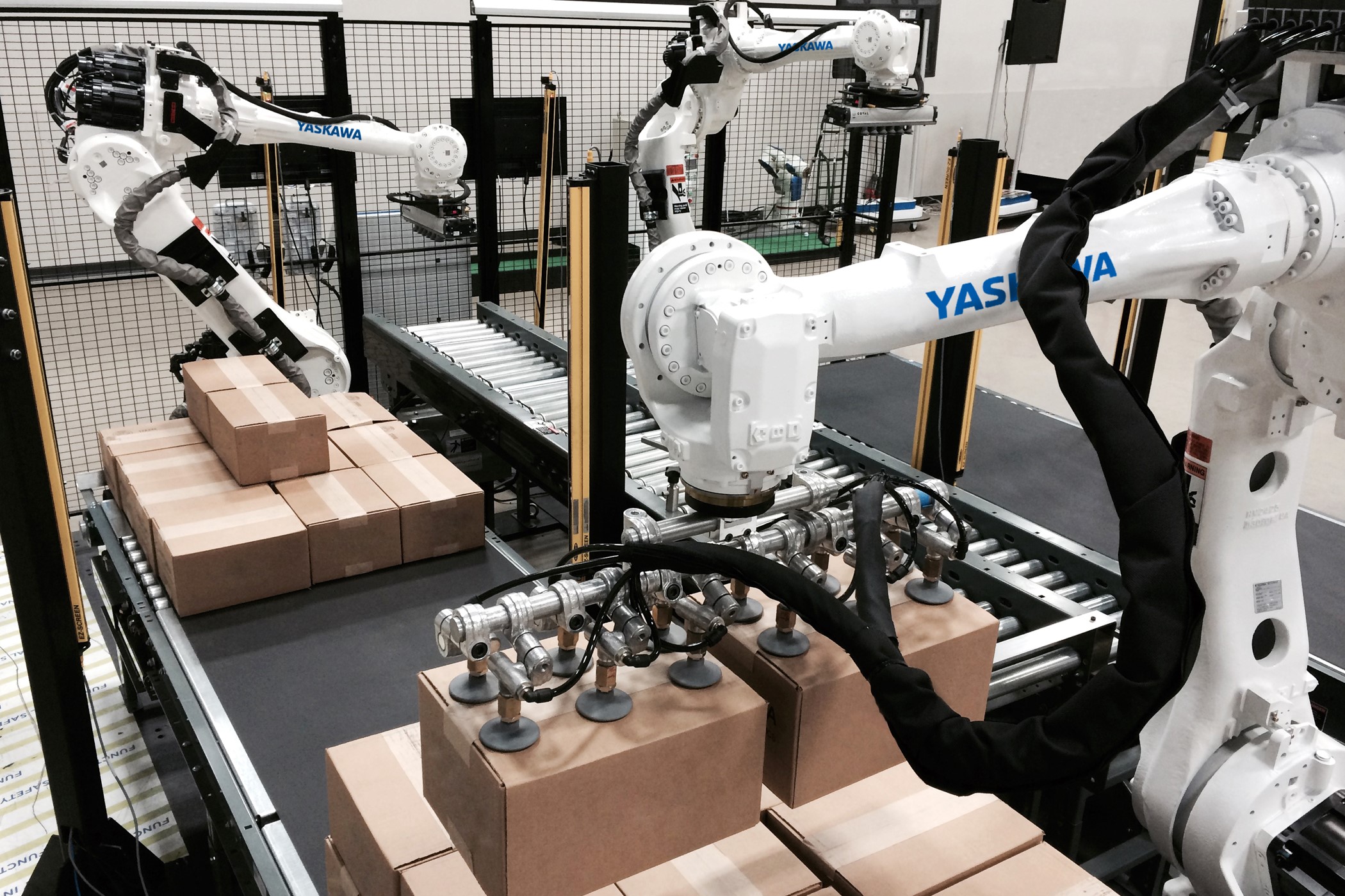
INDUSTRIAL ROBOT Palletising BY AUTOLINE
Autoline excels in Industrial Robotic Palletising, seamlessly integrating products through infeed conveyors into designated palletising cells. Here, our industrial robots execute precise programming to arrange items on pallets, adhering to set patterns and configurations.
Our systems showcase outstanding adaptability, capable of palletising single or multiple production lines concurrently. This dual functionality not only reduces costs but also significantly boosts productivity and manufacturing capacity. Palletising cells are equipped with value-added features like pallet dispensers, slip sheet insertion tools, and shrink-wrapping stations, ensuring a fully automated palletisation process.
Industrial Robot Palletising represents a rapidly advancing frontier in robotics. It outperforms manual palletising with superior speed and safety. Furthermore, these systems are lauded for their flexibility and space-saving design, surpassing fixed machinery options.
Autoline’s palletising robots feature certified food-grade lubricants, rendering them suitable for diverse industries and environments including food and beverage, warehouse and distribution, and industrial product settings. This ensures compliance and effectiveness in a wide array of applications.
INDUSTRIAL VS COBOT ROBOT PALLETISING
When deciding between industrial and collaborative robot palletisers and finding the right robotic automation system for your production line, there are four main characteristics to consider. Industrial Robot Palletising offers unmatched efficiency and precision in handling heavy loads and high-volume palletising tasks. Unlike collaborative robots (cobots), industrial robots excel in heavy-duty operations, ensuring consistent performance without breaks. They can accommodate multiple production lines simultaneously, significantly enhancing productivity and manufacturing capacity. Additionally, industrial robots can be seamlessly integrated with advanced features like pallet dispensers and shrink-wrapping stations for a fully automated process. While cobots offer flexibility and safety in collaborative environments, they may not match the speed and robustness required for demanding palletising applications. Therefore, for industries with high-volume and heavyweight palletising needs, Industrial Robot Palletising stands as the superior choice.
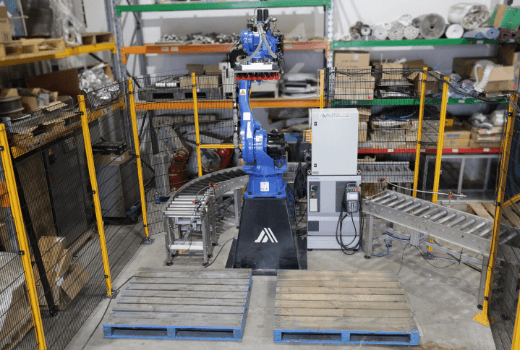
1. Payload
Number one is how much weight do you require the robot to lift?
Industrial robots have higher payloads than Collaborative robots do. Doosan has a heavy range of collaborative robots (cobots) which are called H-Series, these are the most powerful cobot in the market, with an outstanding payload of 25kgs. Yaskawa Motoman has a wide range of industrial robots with maximum payloads and reaches, therefore payload is not often a problem for industrial robot palletising. In summary, if you are trying to lift a payload that is greater than 25kgs, you would need to consider looking at an industrial robot palletiser solution rather than a collaborative one.
2. Reach
The next consideration is reach, how high do you need to stack your boxes on the pallet?
The H Series models from Doosan have a reach of 1500mm and 1700mm which is outstanding flexibility for the powerful payload of 20kg and 25kg! Once your required reach is above the maximum reach for the collaborative robot arm, it may be difficult for a collaborative robot to meet your needs. In this case, industrial robots have larger reaches and would likely suit the application better.
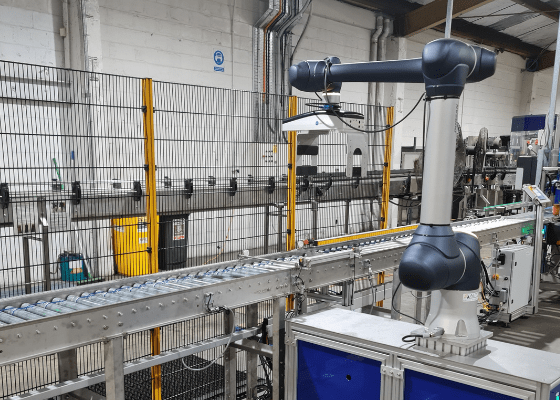
3. Workspace
The third consideration is what space do you have available on your production floor?
A collaborative robot palletiser has a smaller footprint than an industrial robot palletiser system and takes up less physical space. Cobot palletisers also don’t require any guarding due to the industry’s best collision sensitivity powered by 6 torque force sensors, this allows humans to work alongside the collaborative robot safely. Whereas Industrial Robots require full safety guarding and sensing around the perimeter of the footprint to protect humans. It depends on the layout of your production line and floor space you have to determine whether an industrial robot or a collaborative robot would suit your palletising application best.
4. Speed
Lastly how fast do you require the robot to run per cycle?
Industrial robots and collaborative robots have similar cycle times, the reason that industrial robots can handle such high volumes is due to their higher payload capacity. Depending on the weight you are trying to lift, industrial robots can lift a whole layer of boxes or bags in a cycle whereas typically a collaborative robot only lifts one to two boxes at a time.
Yaskawa Robotics
Yaskawa Motoman offers manufacturers a wide range of robotic solutions for palletising and depalletising. Yaskawa robotic palletizers are designed for speed, durability and cost-savings – enhanced by application-enabling software and vision capabilities to help you to tackle simple to complex palletising jobs. The palletising robots range from 50 kg to 800 kg payload with 4-6 axes of articulation. With this wide range of payload capacity, it’s your choice to pick single-case or an entire layer for stacking and breaking down pallet loads. All of Yaskawa palletizer robot models are compatible with the Yaskawa MLX package, allowing you to program them and run Yaskawa’s PalletSolver software directly from your PLC.
DOOSAN ROBOTICS
Doosan have a H Series range of collaborative robots which are the most heaviest payload cobot on the market. With an outstanding 25kg payload and 6 torque sensors, brings a safe work environment for a palletising application. The Doosan H Series Cobots are in a class of their own. Other cobot brands like Universal Robot do not have compatible specifications. The UR20 is Universal Robots’ newest model cobot and this has a 20kg payload and a 1700mm reach. This model is the heaviest payload available at Universal Robots. It still falls short of the Doosan H-Series 25kg payload capacity. Universal Robots has a lower payload and reach range. UR offers a range of 500mm to 1700mm, compared to the Doosan H Series 1500mm to 1700mm reach, the Doosan Cobots is a clear winner.
INDUSTRIAL ROBOT Palletising ENQUIRY
Talk to the Robotic Palletising Experts at Autoline to discuss your current end of line process and find out how a industrial robot palletising system can help you increase your profitability, giving you a competitive edge in your industry.