Your One Stop Robot Welding Shop
Autoline, the premier single-source provider for robotic welding solutions, specialises in bringing world-leading robot brands and cutting-edge welding technologies to New Zealand’s manufacturing industry. By investing in Autoline’s comprehensive solutions, manufacturers receive everything from robot manipulators, welding power sources, wire feeders, torches, and consumables to robot operator training and support. This ensures a seamless integration of advanced manufacturing technology, overcoming labour shortages, meeting increased production demands, and consistently delivering high-quality welds. Whether it be industrial or collaborative robot welding, heavy-duty or welding small parts, MIG to Aluminium welding, Autoline ensures a tailored solution to meet your diverse welding requirements.
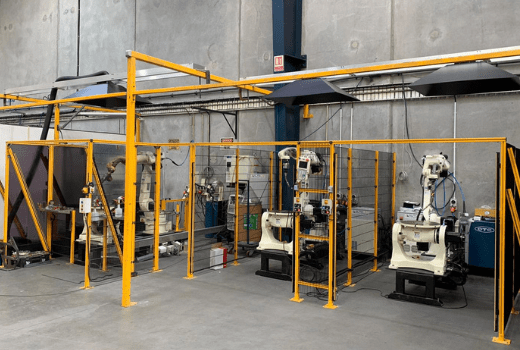
Robot Welding Key Benefits

quality improvement with consistency and repeatability
Robot welding ensures quality improvement with consistency and repeatability by executing precise and standardised welding processes, eliminating the variability inherent in human work. The automated precision of robot welding results in consistently high-quality welds, enhancing overall product quality and reliability.
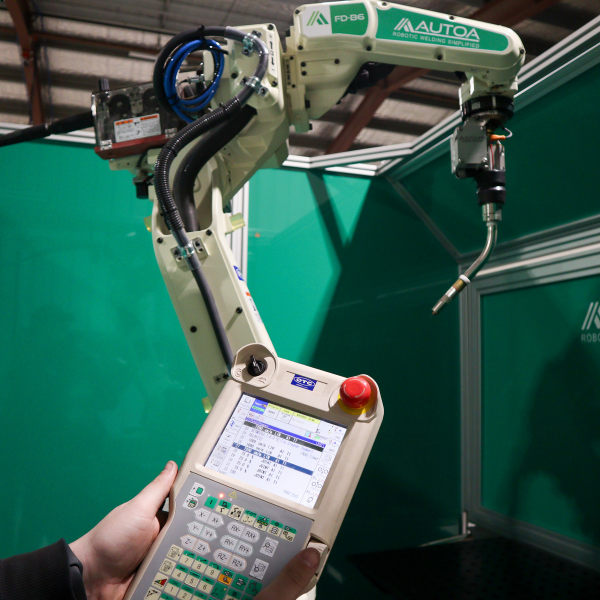
increase productivity and output
Robot welding enhances productivity and output by executing tasks with precision, minimizing downtime, and maximizing efficiency. Its extreme accuracy accelerates welding, simultaneously reducing labor costs and increasing overall productivity.

lower production costs
Manual welding of repeated parts leads to inconsistencies due to human error, increasing the likelihood of rework and consequently raising production costs. In contrast, precisely programmed robot welding ensures certainty in consistent, high-quality welds, significantly reducing rework needs and lowering overall production costs for enhanced profitability.
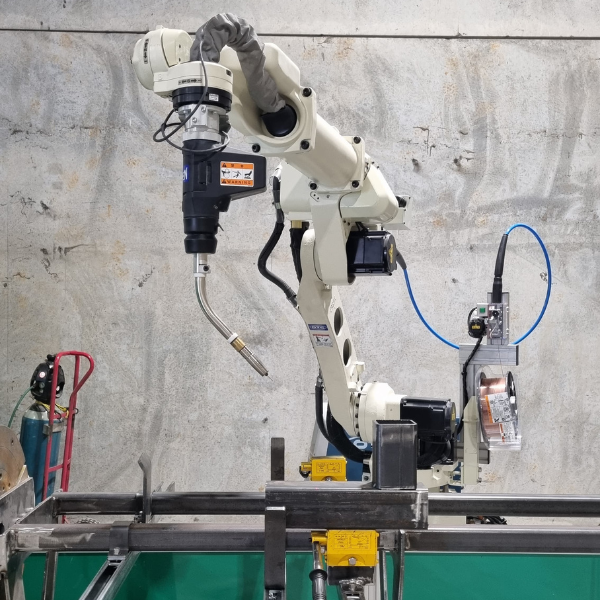
Consumable savings
Robot welding optimizes consumable usage, precisely controlling welding parameters to minimize waste and achieve optimal efficiency. Typically, it saves around 15% on welding gas and wire consumables, contributing to significant cost savings.
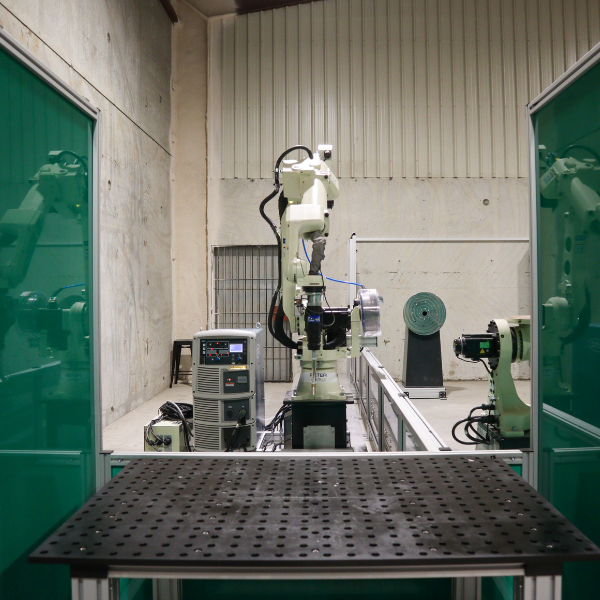
increased flexibility and efficiency
Robot welding facilitates increased flexibility and efficiency by seamlessly adapting to diverse welding tasks, swiftly adjusting to varying production demands, and executing complex operations with precision, resulting in a more agile and productive manufacturing process.
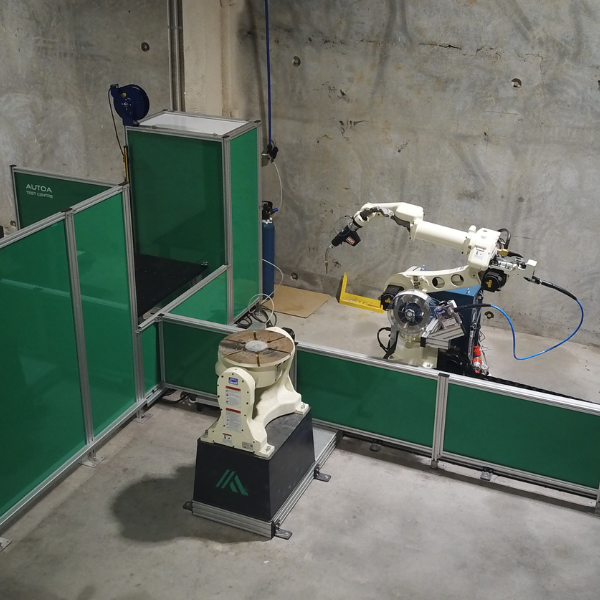
Improved Employee health and Safety
Investing in robotic welding automates high-risk tasks, freeing employees for more skilled responsibilities. A robotic welder reduces workers’ exposure to hazardous conditions, promoting employee health and safety while ensuring a safer work environment with minimal risks of accidents or injuries.
AUTOA Robotic Welding Cells
Emerging from the innovative legacy of Autoline Automation, Autoa is a forward-thinking brand with a laser focus on “Robotic Welding Simplified.” With over 30 years of industry experience, Autoline has consistently pushed the boundaries of technology, carving a reputation for groundbreaking solutions in automation and robotics.
Founded in New Zealand, Autoa is dedicated to meeting the distinctive manufacturing requirements of the Australasian market. Our state-of-the-art Autoa Cells are designed and built in New Zealand, ensuring the highest quality and performance.
In a strategic move to offer customers maximum flexibility and compatibility, Autoa collaborates with renowned robotics manufacturers OTC Daihen and Yaskawa. Our modular approach allows clients to integrate any brand of welding power source seamlessly, making Autoa Cells a versatile solution for a wide range of applications.
Underpinned by Autoline’s rich history of innovation, Autoa is committed to revolutionising the engineering productivity landscape through advanced robotics and relentless dedication to customer satisfaction.
World Leading Robot Brands
Autoline is proud to represent multiple world-leading robotics brands in New Zealand that provide numerous options and systems for robotic welding.
Robot Software
Robot Operator Training and Servicing
Robotic Welding Enquiry
Talk to the Robotic Welding Experts at Autoline to discuss your current welding processes and find out how a robot welding system can help you increase your profitability, giving you a competitive edge in your industry.