New Zealand has always been known for high-quality produce and exports. That’s why it’s important that we embrace automation strategies like robot and cobot palletising. Automation not only streamlines production processes but also enhances food safety standards, reduces wastage, and meets the ever-growing demand for our products on a global scale.
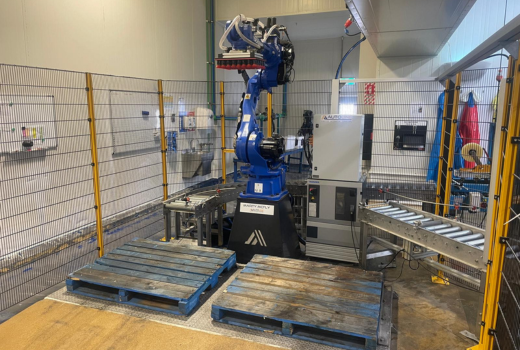
Robot Palletiser
Palletising robots have emerged as game-changers in the food and beverage industry. In an environment where precision and efficiency are extremely important automation is key. Robot palletisers arrange products onto pallets with incredible accuracy, ensuring that food items, beverages, and packaging materials are handled with care.
These robots not only boost productivity but also enhance workplace safety by taking on physically demanding tasks. Moreover, the consistent and reliable performance of robot palletisers significantly reduces errors and waste, contributing to cost savings and maintaining the high-quality standards that consumers expect from food and beverage manufacturers.
Cobot Palletiser
The food and beverage industry is dynamic and competitive. Collaborative robots, or cobots, have since become a versatile partner for efficiency and flexibility. These adaptable assistants are revolutionising palletising processes by working seamlessly alongside human operators.
Cobots are designed to safely handle a wide range of tasks, including precise stacking of products onto pallets. Their user-friendly interfaces and advanced sensors enable them to collaborate with human workers effortlessly, making them ideal for tasks that require agility and dexterity.
In an industry where change is constant and customisation is key, cobots shine for being able to adapt to varying packaging sizes and configurations. With their ability to boost productivity and ensure consistent quality, cobots are swiftly becoming indispensable allies in the food and beverage sector.
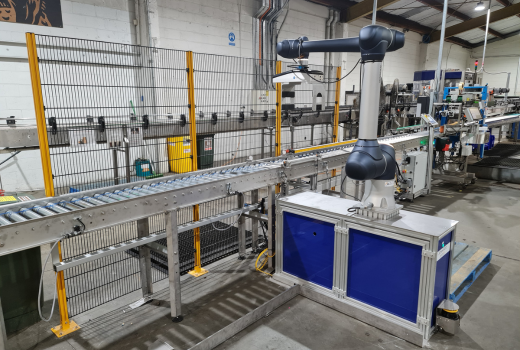
Cobot vs Robot Palletising
Among the innovative solutions available, cobots are making a significant impact on palletising processes. Cobots bring a unique blend of collaboration, flexibility, and safety to the table. Below, we delve into three key reasons why cobot palletising is gaining prominence in the food and beverage sector.
- Collaborative Efficiency: Cobots are designed to work alongside human operators, enhancing overall efficiency on the production floor.
- Flexibility and Adaptability: Cobots can easily switch between different palletising tasks, accommodating diverse packaging formats and sizes. This adaptability is crucial for meeting changing market demands and ensuring efficient production.
- Enhanced Workplace Safety: Cobots prioritise safety, featuring built-in safety features such as collision detection and force-limiting capabilities. This focus on safety not only reduces the risk of accidents but also improves workplace ergonomics by handling heavy or repetitive tasks, thereby reducing the physical strain on human workers and minimising the potential for injuries.
If you’re ready to transform your food and beverage palletising operations with the power of collaborative robots, Autoline is your trusted partner! Contact us today to explore our innovative cobot palletising solutions tailored to meet your exact needs.
Experience the benefits of increased efficiency, workplace safety, and adaptability that Autoline’s cobots bring to the table. Let’s work together to revolutionise your production process and drive your business forward with the latest in automation technology.