Manual palletising is a heavy and repetitive process with a high percentage of lifting injuries in the manufacturing sector.
Investment in robotic palletising helps manufacturers manage many challenges in the industry, including labour shortage issues, increased demand for production and workplace health and safety.
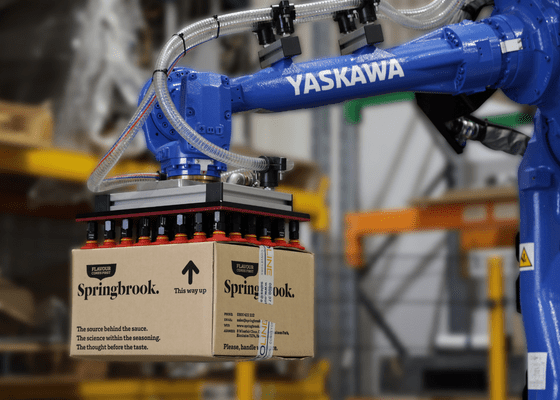
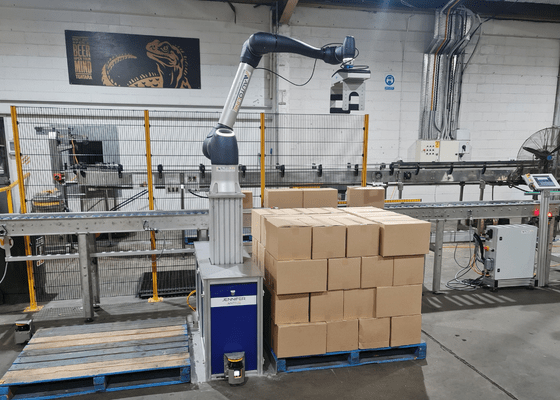
Industrial Robot vs Collaborative Robot Palletising
When deciding between industrial and collaborative robot palletisers and finding the right robotic automation system for your production line, supplier Autoline says there are four main characteristics to consider: payload, reach, workspace efficiency and speed.
What Is Your Required Payload?
Doosan’s heavy range of collaborative robots (cobots), named H-Series, is the most powerful cobot on the market, with an outstanding payload of 25kgs.
On the other hand, Yaskawa Motoman has a wide range of industrial robots with higher payloads and reaches.
If you are trying to lift a payload that is greater than 25kgs, you would need to consider looking at an industrial robot palletiser solution, rather than a collaborative one.
How High Do You Need To Stack Your Boxes On The Pallet?
The H-Series models from Doosan have a reach of 1500mm and 1700mm – outstanding flexibility when coupled with its powerful payload.
Industrial robots have larger reaches, so are a better option if your required reach is above the maximum reach of a collaborative robot arm
What Space Do You Have Available On Your Production Floor?
A collaborative robot palletiser has a smaller footprint than an industrial robot palletiser system and takes up less physical space.
Cobot palletisers don’t require any guarding due to the industry’s best collision sensitivity system, powered by six torque force sensors, which allows people to safely work alongside collaborative robots.
Industrial robots require full safety guarding and sensing around the perimeter of the footprint to protect people.
The configuration of your production line and available floor space ultimately determines which option will suit your palletising application best.
What Is Your Production Line Speed?
Industrial robots and collaborative robots have similar cycle times, but with a higher payload capacity, industrial robots can handle higher volumes.
With their ability to work alongside humans safely and higher payload capacity which increases production speed, ensures quality, and gives flexibility, cobot palletisers will be hugely beneficial in many manufacturing environments.
Industrial robot palletising solutions offer greater speed and payload flexibility – at the cost of a larger footprint and requirement of physical safety guarding.
From industrial robot palletisers to collaborative robot palletisers, Autoline can offer a solution to meet your palletising requirements.