In the fast-paced world of engineering, where precision and efficiency are paramount, a significant challenge has emerged: a shortage of skilled labour. New Zealand’s engineering sector, a vital contributor to the nation’s economy, has been grappling with this issue. However, collaborative robot welders, or “cobots” are a fantastic solution.
The engineering industry is facing a pressing challenge – a shortage of skilled welders. Companies across the sector are struggling to find qualified personnel, leading to difficulties in meeting production targets and timelines. The scarcity of skilled labour not only hampers the industry’s growth but also places added stress on existing workforce capabilities.
Amid this labour shortage, collaborative robot welders, or cobots, are emerging as a innovative solution. These advanced machines are engineered to work alongside human workers, executing intricate welding tasks with unparalleled precision and consistency. This innovation brings a ray of hope to an industry eager to maintain its competitive edge.
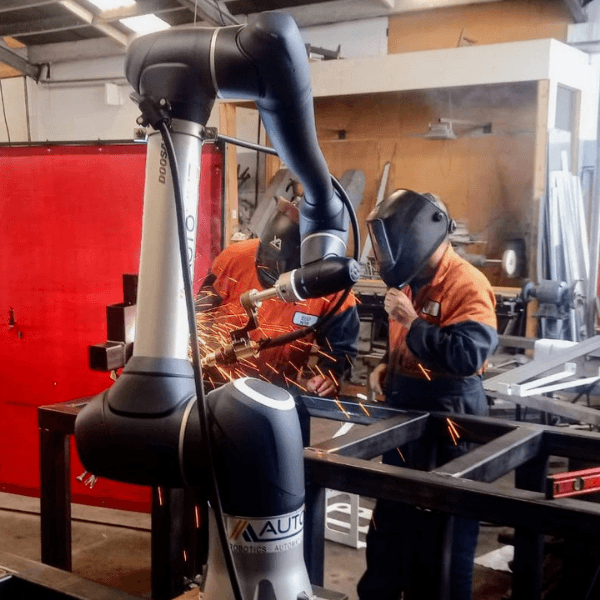
The Benefits of Cobot Welders:
- Increased Productivity: Cobots are designed to work tirelessly, operating 24/7 without fatigue. Their tireless nature significantly increases productivity and output, allowing companies to meet demand and expand their market presence.
- Consistent Quality: One of the most noteworthy advantages of cobot welders is their unwavering ability to produce uniform welds. This consistency reduces errors and the need for costly rework, ensuring top-notch quality in the final products.
- Skill Amplification: Rather than seeking new skilled hires, companies can leverage cobots by training their existing workforce to program and collaborate with these machines. This upskilling approach amplifies the skills of current employees, creating a more versatile and adaptable team.
- Safety Enhancement: Cobots are engineered with advanced safety features, allowing them to operate in close proximity to human workers without posing significant risks. This collaborative environment enhances workplace safety while maximising efficiency.
Luge Cart World harnessed Autoline’s Cobot Welder to refine their manufacturing. Internalising welding defied expectations, accelerating processes, boosting control, and trimming costs. Designed for low-volume, high-mix manufacturing, Autoline’s cobot welder proved invaluable to Luge Cart World. Chairman Les Osbourne emphasised, “It was definitely worth the investment. The Cobot welder is a valuable asset.” Click here for the full testimonial.
Cobot technology is not only changing the face of engineering but also shaping the skills landscape. Existing workers can now learn how to program, maintain, and collaborate with cobots, expanding their capabilities and making them more adaptable in an evolving industry.
It’s essential to note that cobots are not intended to replace human workers, but rather to enhance collaboration and optimise workflows. By delegating repetitive tasks to cobots, human workers can focus on tasks that require creativity, decision-making, and complex problem-solving, adding unique value to the workforce.
Cobot welders are revolutionising the NZ engineering landscape by addressing the critical labour shortage. These advanced machines not only increase productivity but also foster a culture of innovation and collaboration. As cobots become an indispensable part of the sector’s growth, the future of NZ’s engineering industry looks promising.
To learn more about cobot technology, training opportunities, and upcoming industry events focused on automation and robotics, browse our website or contact us. Embrace the future of engineering with cobot welders and join us in shaping a more productive and innovative industry.